|
|
CSM-1 FIXED SPEED
CHARPY SPECIMEN MILLING MACHINE
The Fixed Speed Machine is recommended for customers who
are producing specimens in carbon steels, easily machined
low alloy steels, non-ferrous and plastic materials. This
machine
has a fixed cutter speed of 1.98 m/sec and a variable feed
rate for the samples of 2.5-9.0 mm/sec.
For customers producing specimens in a wider range of
materials, see the CSM-1V with variable cutter
speed
|
CSM-1V: VARIABLE SPEED
CHARPY SPECIMEN MILLING MACHINE
The Variable Speed Machine is recommended
for customers who are producing specimens in carbon steels,
more difficult to machine alloy steels, stainless steels,
non-ferrous and plastic materials.
This machine has a variable cutter speed of
1.0-2.5 m/sec and a variable feed rate for the samples of
2.2-9.0 mm/sec.
The varying of the cutter speed for differing materials
improves the cutter tip life.
|
A
D.C. thyristor drive control provides the variation in speed
of the rotary fixture, for both the
Fixed and Variable Machines.
The fixture speed sets the feed rate which the samples are
machined.
|
An
A.C. thyristor drive control provides the variation in
thecutter speed, on the
Variable Machine only.
|
|
Work Holding Fixture:
The circular fixture allows up to four specimens to be
machined during the same operation.
Various clamps, anvils and clamping screws are available to
suit the type of rough cut blanks being used.
One circular fixture is included with each machine. For
maximum machine production a 2nd fixture (optional extra) is
recommended, so that whilst the 1st fixture is being
machined, the 2nd fixture can have its samples loaded. |
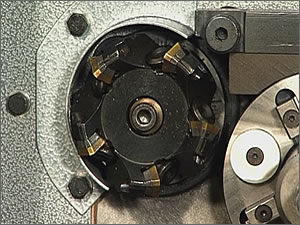
|
Cutter:
The cutter is fitted with five ISO
carbide inserts, which are easily replaceable.
A micro adjuster allows for accurate control of specimen
size and allows for compensation of cutter tip wear.
|
|
|
Fixture:
The rotating work holding fixture is
fitted with clamps, anvils and clamping screws to suit the
type of blank being used, i.e. rough sawn
square/rectangular, round or tubular section and the size of
specimen to be produced, i.e. 10mm square or sub-size. |
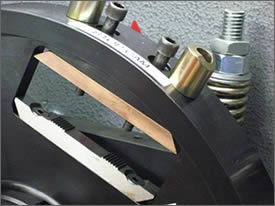 |
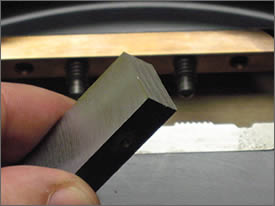 |
|
|
For ease of fitting samples, the fixture is removed from the
machine and placed onto a bench mounted holding bracket, one
bracket is supplied with each fixture.
Up to four rough cut samples may be loaded into the fixture,
which is then re-mounted onto the machine spindle and the
cutting cycle started.
The machine cuts the first side of the samples (1st cut).
The fixture is then removed from the machine, turned through
180 degree and refitted to cut the second side of the
samples (2nd cut).
|
After completion of the 2nd cut, the fixture is removed from
the machine and placed onto the bench mounted holding
bracket.
The samples are removed and remounted into the fixture at 90
degrees. The fixture is then mounted into the machine to cut
the third side (3rd cut). The fixture is then rotated
to cut the fourth side (4th cut), which completes the
production of the 10mm square samples.
Adjustment of the micro-adjuster may be necessary to achieve
the required size and dimensional accuracy of the finish
machined specimen.
|
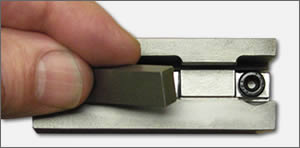
Sub size fixture |